Meeting
November 14, 2009
Meeting - November 14, 2009
We met at Jack Gellerstedt's shop in Forest, VA.
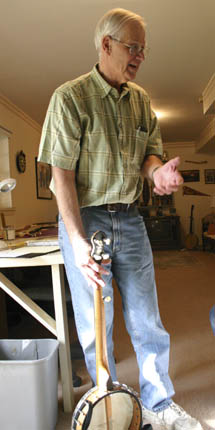
Jack Leads the Banjo Project Discussion
Open Back Banjo Project
Jack Gellerstedt continued a discussion of a banjo project. See the previous discussion from the meeting on October 11, 2009).
The primary focus of the meeting was on open-back banjo construction techniques and plans for a possible club banjo project.
Options for the Rim
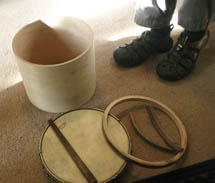
Woody's right foot is pointing to a drum shell that can be sliced into banjo rims.
Jack showed us some options for making the rim. One is using a drum shell, slicing off a piece of the desired size. Another is steam bending the rim either in one piece with a scarf joint, or in multiple sections. He steam bent some small pieces as a test (quarter circle pieces seen in the drum shell picture). Still another option is building up the rim in multiple, thin laminations. This is the way the drum shell is built. A potential disadvantage of this method is that multiple laminations require a large amount of glue that may adversely affect the sound.
Cutting the Neck Profile
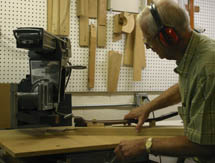
Jack shows how he cuts the neck radius.
Detail of the setup is shown below. The pivot point of the fixture is centered under the arbor shaft. This technique will work for any radius larger than the radius of the saw blade.
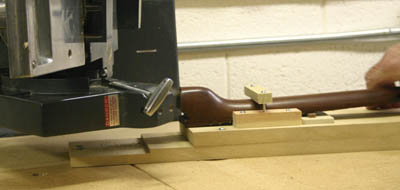
Project Decision
We decided that in lieu of a club banjo project we will work on individual banjos together for each member who wants to build one. The primary work will be done by each individual in their own shops, and they will buy their own parts. On certain things we will work together to make use of special equipment and to allow common setups. So far, we have three members who will make banjos: Dennis McKim, Larry Sakayama, and Jack Gellerstedt. Work will start soon, but probably not until after the holidays. Dennis, Larry, and Jack will confer to get things started. Also, we'll try to do some of the common operations at a regular meeting so others can view techniques and participate as well.
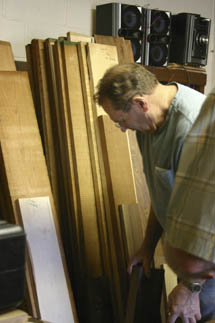
Larry Cagle at Lynchburg Hardwoods
Visit to Lynchburg Hardwoods
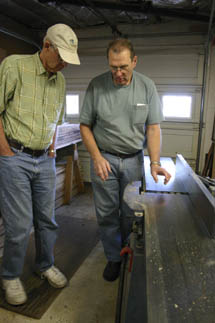
Jack listens as Larry Cagle explains the 10" jointer
After the regular meeting we went to Lynchburg Hardwoods, a supplier of hardwood lumber and services operated by Larry Cagle. He specializes in domestic and imported lumber, kiln dried and graded. He had some exotic woods - bubinga, purple heart, zebrawood, mahogany, as well as maple, oak, walnut, cherry, and others. He also provides custom furniture, repair, refinish, molding, planing, sanding, and lathe work services. He has a well equipped facility, but his business is small enough to provide personal services to the hobby wood worker and luthier, as well as professionals.
You can contact Lynchburg Hardwoods - Larry Cagle by phone at 434-239-1344 or email him at ljcagle@comcast.net.
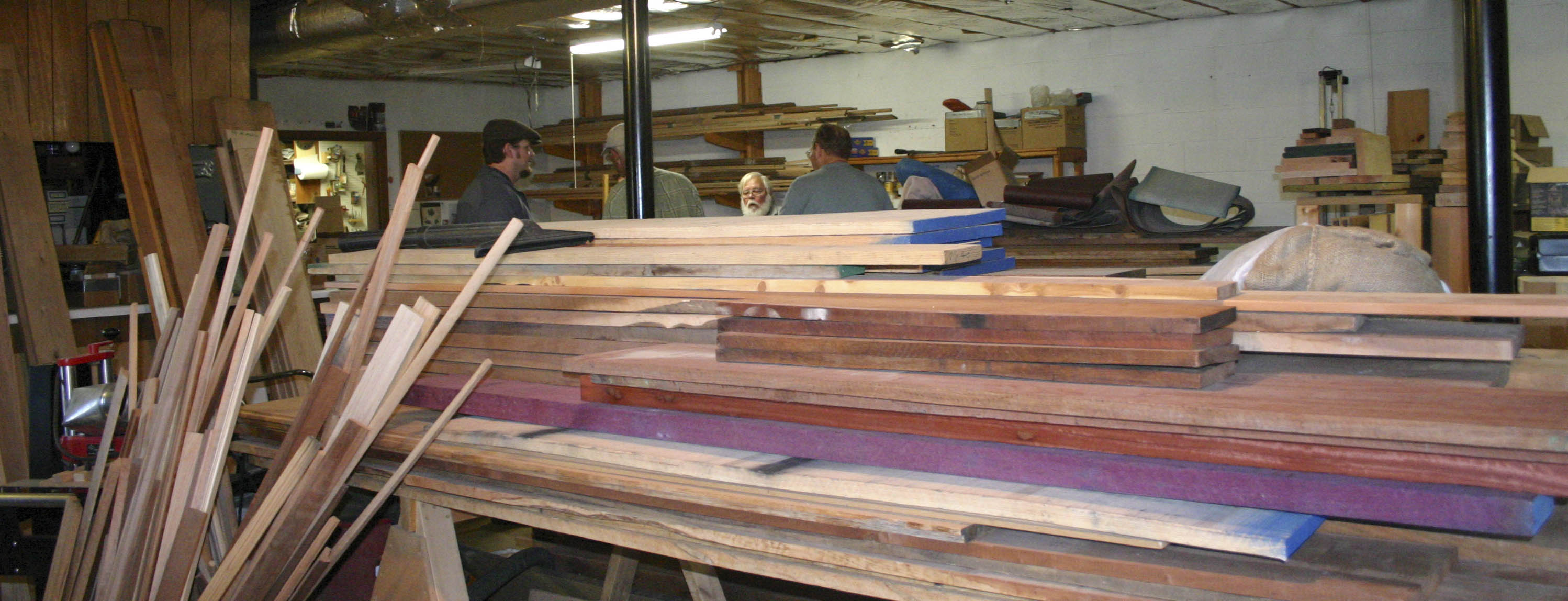
Jack's Trailer
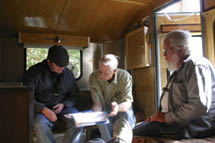
Jack and his brother built the trailer.
The photo shows B.B., Jack, and Dan inside the trailer.
More information on the trailer is coming if Jack ever decides to send it.